Lessons Learned from Living Lab
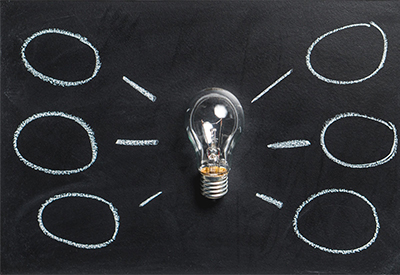
April 7, 2020
By Steve Mesh
In 2007, a new headquarters building for the New York Times was completed in midtown Manhattan. State-of-the-art lighting and control equipment were deployed. This was described in Wikipedia as follows: “In a normal office building, lights usually consume about 44% of total energy. The NYT building uses less, because its design, lighting, and shading systems allow the sun to be the main source of light. Each of the more than 18,000 electrical ballasts in the lighting system contains a computer chip, allowing each room’s lights to brighten or dim depending on whether a room is occupied and how bright the sun is.”
In fact, this was a deployment of a digital, wired networked lighting control (NLC) system. The “base building” luminaire was a recessed, single-lamp T5 fluorescent downlight. The Department of Energy (DOE) realized that this was a great opportunity to investigate the energy-savings potential of using state-of-the-art lighting and control systems. Lawrence Berkeley National Labs (LBNL) was asked to study the effect of this technology by metering the lighting system over a period of time. It was determined that using the digital, wired NLC system resulted in a 38% overall savings from max connected load. Holy cow!
Several years later, DOE decided that it would be great to study the same thing … state-of-the-art lighting and controls equipment … but this time when they are deployed in retrofit situations. To that end, LBNL secured the cooperation of two companies with large office buildings in NYC. Ultimately, only one installed equipment for study. One floor of a large office building located downtown near the Freedom Tower was allocated for this project. Each of four quadrants got new pendant direct/indirect LED luminaires (to replace the existing T5 fluorescent fixtures), a new NLC system, and in some cases new automated window shading systems.
Even though this was a recently completed Class A office building in Manhattan (finished in 2009), the work was in fact done on a true retrofit basis. Why? The floor in question was not “gut rehabbed”. It was an occupied floor and the electrical contractor was only allowed to do the installation work at night. I worked on the project as a consultant to LBNL. One of my major responsibilities was to be on-site during a portion of the installation to observe how easy (or how hard) it was for the electrical contractor to install this new equipment. I spent 18 different nights being an “observer”. Ultimately, all of the new equipment was successfully installed, and both the new LED fixtures as well as NLCs accounted for substantial energy savings. That’s remarkable, considering that these systems were installed in 2015 and the equipment they replaced was only six years old!
However, the question remained – how easy was it to install this new equipment on a retrofit basis? Answer – fairly easy! Having said that, I observed a variety of things during the course of the installation that were eye-opening to me. I am a virtual expert on networked lighting control systems (or at least I play one on TV!). I had also used two of the four NLCs in hands-on classes, so I was well-versed in how to wire and commission them. The installing contractors were not. They were really great guys and very capable electricians. They simply didn’t have prior experience with this type of equipment. This was the exact point of the research project! Here are some of the more interesting takeaways I had from my 18 nights of observation (in no particular order of importance):
- Controllers wouldn’t fit into luminaire housings – In one quadrant, the luminaire vendor said that there wasn’t enough room in the housing for the NLC system’s “controllers”. As a result, the controllers had to be remotely installed in the plenum. Because the owner wanted the uplight and downlight components to be separately controlled, that necessitated using two controllers (and two drivers) for every luminaire. When I opened up one of the fixtures on-site, it was clear that there was plenty of room for about 20 controllers in the housing!!! I can only assume that the fixture vendor didn’t want the hassle/responsibility/potential liability of incorporating a device from a separate vendor into their fixture. The resulting wiring between the remote “controllers” in the plenum … down the power cords … and to the drivers embedded in the fixture was quite complex. Some miswiring did in fact occur and that caused some friction between the installing contractor and various vendors. If the fixture vendor had pre-installed the NLC’s controllers in the fixtures – in the factory – then the electrical contractor would only have had to bring one set of power wires (black, white and green) to each luminaire! What a shame. Moral(s) of the story? 1)Consider using fixtures and NLCs where both vendors belong to the same conglomerate, to avoid finger-pointing. Or at least consider selecting fixtures where the vendor has an established relationship with controls vendors who you are likely to pair with those fixtures. Many do. 2.) If possible, get actual samples of proposed luminaires during the specification process. If that’s not possible, at least ask for drawings so you can determine if controls components can fit in the luminaire housing. If we had such drawings in advance, it would have been incredibly clear that there was plenty of room to pre-install these components in the housing – eliminating the need for much more complex and time-consuming wiring to remotely-mounted devices. And it would have made it much easier for the owner and everyone else involved to press this point with the luminaire vendor.
- Job-specific wiring diagrams weren’t always provided – As mentioned, the owner wanted the uplight and downlight components to be separately controlled, necessitating two controllers and two drivers for every luminaire. In addition, each NLC had different methods of providing lighting for emergency egress. Last but not least, in some of the quadrants, the controllers and/or drivers were remotely mounted in the plenum as previously described. In some cases, the NLC vendor only provided typical wiring diagrams – for example, the type of diagram that might be included on a cut sheet. Invariably, those diagrams do not show atypical conditions. Nor do they typically show wiring required for providing emergency egress lighting. It was very surprising to show up on the job site during the first night of installation and realize that the electrical contractors didn’t have “job-specific” diagrams for all of the NLC systems! Morals of the story? ) NLC vendors should always expect (and be asked) to provide “job-specific” wiring diagrams! 2.) Electrical contractors should always ask for such “job-specific” wiring diagrams prior to starting their work! Since the specific contractors in question didn’t have prior experience installing NLCs, and in some cases didn’t have job-specific wiring diagrams and instructions, some “demystifying” was required. I was able to provide that. But that was only by pure happenstance since I was on-site to observe the installation. Installing these systems is not “rocket science”! But if an installing contractor hasn’t had prior experience with NLCs before, at the very least they need a minimum amount of information, help and hand-holding to guarantee a successful installation.
- Proprietary cable wasn’t on-site at the start of installation – One of the wired NLC systems required the use of a specific type of cable for connecting “standalone” devices like photosensors, occupancy sensors and switches. It turns out that this cable wasn’t on-site on the night that the contractors expected to start installing this equipment. Why not? Because no one had read the note on one of the drawings saying that the contractor had to order this cable separately from the rest of the system’s components. This is a common practice, because the controls vendor has no way of knowing how many feet of cable will be required on a particular project. So instead of supplying many more spools than are necessary, they ask the contractor to order this separately. This is one of the things that “slipped through the cracks”. Since this cable wasn’t ordered in advance, the contractor was only able to install the luminaires during the initial period of installation in this quadrant. Because this was retrofit work – performed at night – everything had to be buttoned up so the employees could work normally the next day (ceiling tiles reinstalled, debris cleaned up, etc.). So the electricians came back on a later date once they had the spools of cable and completed the “networking” of peripherals. Moral of the story? ) Regardless of whether you are doing an installation of an NLC in new construction or in an existing building, someone has to be the point person to make sure “I’s” are dotted and “T’s” are crossed! That could be anyone who has the technical knowledge required – a lighting designer, electrical engineer, knowledgeable sales rep, and/or anyone else. But someone has to do it!!! Not doing so can have an adverse effect on A.) delays in completing the installation, B.) callbacks, C.) cost adders for labor and/or equipment, D.) additional disruption to the space, occupants or ceiling tiles, etc. Therefore, doesn’t it make sense to designate someone as the point person to insure adequate coordination throughout the entire process? I would say so.
- Some luminaires were supplied with non-standard wire colors – In some quadrants, NLC luminaire “controllers” had to be remotely-mounted in the plenum. In one quadrant, due to the very minimal fixture design, the LED drivers also had to be remotely-mounted in the plenum since there was no way to incorporate them into the housing. At least one of the luminaire vendors supplied power cords (like SJ cable) with non-standard wire colors! One of the two power cords already contained five conductors (hot, neutral, ground, and two for the 0-10V dimming circuit). Therefore, the second cable only needed four conductors (hot, neutral, and the two 0-10V wires). In that second cable, the conductors were colored-coded as follows: red – line voltage power to the driver; white – neutral for the power to the driver; black – 10V (for the dimming circuit); green – 0V (for the dimming circuit). There was also labeling on each cable, but it was either wrong or misleading. The color-coding should have been as follows: black (or orange) – line voltage power to the driver; white – neutral for the power to the driver; violet – 10V (for the dimming circuit); gray – 0V (for the dimming circuit). My gosh … if you want to dramatically increase the probability of the contractor miswiring things on the job site, use non-standard wire colors and provide misleading or inaccurate labels for conductors! Moral of the story? Don’t do that!!! How could this be avoided? Ask for submittal drawings (and/or samples!) for approval, including all details such as wiring – showing color-coding, labeling, etc.
As mentioned earlier, ultimately all equipment was successfully installed and commissioned. And the resulting energy savings from the six-year-old existing luminaires and controls was substantial. However, even in this Class A office building in downtown Manhattan, a variety of issues reared their ugly heads during the installation! Nothing that couldn’t easily be fixed, mind you! But the question remains – what can you do to insure a successful deployment of an NLC in a retrofit situation (or even for that matter in new construction)? My three major takeaways from this experience are as follows:
- Training programs – Develop educational offerings, such as the California Advanced Lighting Controls Training Program (CALCTP) and the DLC’s Advanced Lighting Controls Training Class, to educate electrical contractors and others about NLCs. Some vendors also have good classes for their own products. If you are an NLC vendor, considering offering training on your products – especially hands-on training. If you are an electrical contractor, seek out such classes offered by vendors or others. You can find details for the CALCTP program at https://www.calctp.org. The national version of that is NALCTP (https://www.nalctp.org). You can get more information about the DLC class at https://www.designlights.org/lighting-controls/training-programs/.
- Project management – Designate one party up-front to develop workflow, set target dates, communicate with team members and vendors, etc. Regardless of who this person is – internal staff, sales representative or others – there must be at least one person who can dot every “i” and cross every “t”. NLC systems are not actually rocket science. However, by definition, they do entail some degree of complexity. On any NLC deployment project, someone needs to be accountable for checking details.
- Project team – Create a list of all required team members. Office lighting retrofit projects will usually require an electrical engineer and/or other specifiers, but so will many other project types. The owner’s IT staff will no doubt need to be involved in an NLC deployment. If emergency egress lighting will be affected by deploying a new NLC system (which it invariably is), then an electrical engineer may be needed to verify compliance with codes. Lastly, there are the contractors who will be installing the equipment, and the vendors. Just because it’s a “retrofit” project, that doesn’t mean that you can or should be casual with the specification and installation process. In some cases, deploying an NLC will impact not only things like emergency egress lighting but possibly more (i.e., rebalancing circuitry, code compliance, etc.). Having an entire team where members communicate with each other throughout the process is a great way to guarantee a successful NLC deployment.
Published with the permission of Lighting Control Association. This article was first published HERE.